
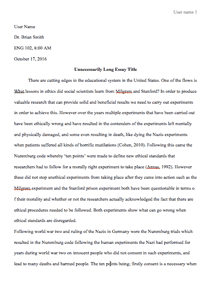
Introduction
The supply of commodities, referred by the general name, Vehicle Routing Problem, is among the most imperative elements of the supply chain. Therefore, the vehicle routing problem (hard combinatorial problem), has attracted substantial research attention and several algorithms are proposed for its solution.
Supply Chain Management refers to the series of approaches used for effective integration between the manufacturers, warehouses, suppliers, and stores, in order for the merchandise to produce and distribute products to the respective locations, at the required quantities and in a timely manner to reduce incidences of systemwide cost at the same time fulfilling the requirements of service delivery (Harrison & Van Hoek, 2008). The key objective of the Supply Chain Management is to be cost-effective and efficient although the whole system, total systemwide cost, starting from the transportation and distribution to inventories of raw materials, work-in-process, and finished goods, are to be minimized.
The Vehicle Routing Problem (VRP) is utilized in the designing of an optimal route from a vehicles fleet for servicing a bunch of customers, provided a group of constraints. In the technical perspective, the VRP is essential in SCM with regards to the goods and services physical delivery. However, there are a number of variants that are related to VRP: they include, the quality of goods and services needed, formulated base on nature of the goods transported, as well as the preferences and characteristics of the customers and the vehicles (Ballou, 2007).
With the growth of the globalization together with the international markets, the supply chain management has acquired elevating attention. The more multifaceted of the underlying production, procurement and distribution activities, together with the increasing capacity of the involved parties, attract the necessity for proper decision support mechanism. The Supply Chain Management (SCM) is made up of various things like the storage and movement of the raw materials, work-in-process inventory together with the processed goods from the origin point (Christopher, 2016). SCM perceived with the involved activities has been distinguished as planning, execution, designing, monitoring, and control of the supply activities, with the purpose of establishing the net value, establishing the competitive infrastructure, influencing of the worldwide logistics, gauging global performance, together with the harmonizing supply with demand. With regards to the chain partners, SCM includes the efficiency integrating manufacturers, suppliers, and store, warehouses such that the merchandise is manufactured and distributed with the appropriate measures to the required locations and at the needed time so as to reduce the system-wide cost, at the same time the requirements of the system levels (Tayur, Ganeshan, & Magazine, (Eds.) 2012). The following report will present models approaches and analysis for solving various distribution problems.
The VRP with Time Windows
It is also abbreviated as VRPTW, it is described on a network G= (V, A0,) Where {1, . . . , n}, V= {0, n + 1};and n+1 are two duplicates of depot, c= = {1, . . . , n} which is denoted as the customer set, and A = {(i, j) : i, j V, i j} is the arc set. Having the arc (I, j) A is related the travel timetij together with the travel cost Cijand the travel and the cost matrices fulfills the triangles inequalities. Having end node, i V is related a demand qip of product pEP that required to be fulfilled by service time Si and one vehicle. Additionally, the time window [ai, bi] is connected with each node, within which service is expected to begin. Earlier arriving vehicles are needed to wait until the starting of the time window as well as the unit penalty CL is incurred from the starting service bi (Tayur, Ganeshan, & Magazine, (Eds.), 2012).
It is made up of finding a collection of routes for m vehicles, in that:
Every route begins and finishes at the depot;
Only one vehicle visits every customer/distributor in a particular stated time window;
The aggregate customers demand allocated to a particular vehicle doesn't surpass its loading competence;
Routes begin then finishes within the working schedule of the driver
Decision Variables
Binary flow variables Xijk equals to 1 if vehicle marked k negotiates from customer I to customer j;
Binary variables yik equals to 1 if vehicle k visits customer I and delivers demand qip for each produce pP;
Time variables Wik 0 define the beginning of service customer I by vehicle kK;
Penalty variable ui0 model the hesitate respective to the beginning of the service of customer i J= {0.1., n,n + 1}, where 0 and n=1 represent the depot,
Si is serving time for customer iMathematic Model
Lotisizing Problem in Production Planning
The lotsizing problem involves optimizing of the tradeoff between the inventory holding the cost and the setup:
When bulk batches of items are produced instantaneously, the involved number of setup operation is reduced. Although, the subsequent inventory stock levels as well as the holding cost increases.
When producing small quantities of the products simultaneously leads to reduced average inventory cost, however, there will be an increase in the setup cost.
The customers can only receive services after all needed products are ready for dispatch and shipment. Once the customer orders are prepared, the better for the departure of the vehicles and distribution of items to customers (Tayur, Ganeshan, & Magazine, (Eds.) 2012).
Two pivotal problem categories emerge in the field of production planning. Firstly, lotsizing decision are established for the determination of a rough production plan considering machine availabilities and resources at aggregated and tactical level. IN this case, a moral comprehensive schedule may be created, whereby, the resource abilities are clearly considered, and viability with regards to their usage as well as the timing of production is taken into account. Usually, these two subproblems have been independently solved. The integrated outlook is significant in occasions where their exits reduced intermediary storage capacity, and there is need to distribute the manufactured products immediately, an event often encountered whereby the goods are highly perishable (Malandraki & Dial, 1996).
The consequent effect of resolving lotisizing problems is typical attempts of optimizing the tradeoff between the inventory holding costs and setup. Manufacturing huge batches of products each time minimizes the encompassed amount of setup operation. Although, there is the rise of the holding cost as well as the subsequent inventory stock quantities (Bard, Kontoravdis, & Yu, 2002). The lotisizing problem may be combined with a downstream supply of chain pattern. Clients can only be attended to after all the needed products are prepared to be dispatched and shipped. Normally application comprises of the produced and delivered subsequently like the delivery of daily newspapers or bakery products that are normally produced during the nightshift. Once the customers orders are prepared, the vehicles ferrying them will depart from the main center of production and supply the items ordered to the customers (Malandraki & Dial, 1996).
Machine Scheduling Problem in Production Planning
Scheduling is a properly studied problem used in the operations management. Varying with the traits of the fundamental process of production, some factors can be differentiated, such as flow shop, job shop, and more particular open shop problems. Scheduling sets at the central heart of operation production planning, whereby the work is supposed to be allocated to the machines, then schedules need to satisfy the number of technical requirements or precedents (Tayur, Ganeshan, & Magazine, (Eds.) 2012).
After the production of the goods, its delivery might be made to the following year of the supply chain, then the transportation may begin once after the completion of the last task in the production process. The scheduling decision interferes with the routing problem decision and vice versa (Harrison & Van Hoek, 2008).
The Lotsizing Problem and Routing ProblemThen let set for time period per day for the production be denoted by T= 1,, T. Then Ct denoted the aggregate capacity for production in t. While Cps and P denote each setup of product p, and the set of products is denoted by P (Pureza, Morabito, & Reimann, 2012).
Decision VariablesVpt0 is the amount of product p that is produced in the time-slot t.
Vpts {0,1) equals to 1 if products p is manufactured in period t;
hpt 0 denotes the stock level of product p at the beginning of period t.
Opkt 0 denotes the quantity of goods of type p to be loaded into vehicle k in the time period t;
Zkt [0,1] is equal to 1 if vehicle k departs the depot at the time t.
Mathematical Model
Mechanic Scheduling and Routing Problems.
The job shop scheduling problem is distinguished by the following aspect:
R is the set of machines
P is the set of products which are processed on machines
The production process for every particular product p made up of the set of tasks Bp
Every task h E Bp must be executed on a particular machine r E R;
Br is the set of tasks for machine r E R;
.Cprthe production cost unit for product P E P.dh is the processing time of task h;
.ep is the initial task of product p.gp is the earliest starting time of product pTasks need to be scheduled on machines in the manner that the sequence of the tasks for every product satisfies precedence requirements (Harrison & Van Hoek, 2008). It is impossible to interrupt the operation of the tasks once it has begun. The objective is to determine a viable schedule, in that, every machine may only handle one task at every single time and the absolute cost of transportation and production of customers demands is reduced (Christopher, 2016).
Decision Variables.Vh0 implies to the production starting time which us associated with task h;
.Zhl [0,1] equals to 1 if task h is performed prior to task l; these variables are extinguished for the entire pairs of tasks...
Request Removal
If you are the original author of this essay and no longer wish to have it published on the customtermpaperwriting.org website, please click below to request its removal: