
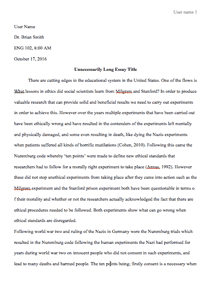
Continuous improvement is the ongoing advancement of products, services or processes through incremental and revolutionary improvements. A never-ending determination to uncover and eradicate root causes of problems. Usually, it involves many progressive or small-step signs of progress rather than one overwhelming innovation. From a Japanese perspective, continuous improvement is the source for their business principles. It includes everyone, management, and labor, in finding and reducing waste in machinery, labor, materials and production methods. Continuous improvement can range from simple changes in the day-to-day workings of a company's projects to major shifts in emphasis and procedures across the whole organization. In all cases, you will require the right tools to achieve success and keep it going. (Inman & Turner, 2017), this shift began following the defeat of Japan in World War II
(International Atomic Energy Agency, 2006) There are several basic organizational systems, structures and roles, which offer a firm foundation for the effective implementation of continual improvement. If these basics are not in place or are deficient, operational execution of a constant improvement program becomes more unapproachable. These improvements include leadership, business planning, accountability, infrastructure, teamwork, project management, communication, oversight, and assessment.
According to Pojasek (2003), opines that lean Six Sigma is an operational philosophy that initially derived from the Toyota Production System. It emphases on shortening the time that passes between a customer's order and the shipment of the product or the provision of the service that fills the order. It is a management concept used efficiently to improve business processes based on blending of the various tools of Lean and Six Sigma. These include faster processes, higher quality, increased customer satisfaction. Cost savings and sales growth and improved employee morale and skills.
In today's global market, competition continues to get harder; it is essential for companies to provide more consistent or better quality products and services to their customers. To provide such classes that meet or exceeds customers' expectations, a key management approach such as total quality management (TQM) approach requires implementation. Total means; involvement and input of everyone in the organization from top management to its employee; quality means, fully meeting customers' needs and requirements all the time and management is the way we act and operate our policies and procedures including training and instruction to all employee. (Kurran, 2007) it's a management philosophy that seeks to integrate all organizational functions such as, marketing, finance, engineering, customer services and other to focus on meeting customer needs and organizational objectives.
Toyota Motor Company has been one of the most successful companies, which have incorporated the two methods of quality improvement. At the corporate level; about TQM, they put the customer first, second, they continuously improve their products also referred to as Kaizen, which means continuous improvement. Third, they foster total participation by encouraging the entire employees to be involved in making solid contributions towards the development of the company and the achievements of its objectives. In fact, the employees get rewards for their contributions.
About Lean Six Sigma, the Toyota philosophies of Kaizen, just in time, and pool system are practiced in every line on every workday and throughout all phases of production. Kaizen means, continuous improvements; and just in time, means suppliers deliver parts and materials, just in time, no delays. In the pool system, vehicles are pulled to meet customer demand not pushed through the plant. Everything starts with the client and vehicles production meets market demand.
In the project level, everything is maximized to produce the least amount of defects and increased quality within a limited amount of time. Robots assist team members in a variety of ways; they paint well and deliver needed supplies to the line. Toyota's philosophy is that machines should help team colleagues in a project not replace them. While the team members are working on a project, placements of vehicles parts are just a few feet away from the team member, who will use them with no waste of time, material or motion. In case there is a defect during production any team member has the authority to stop production at first sight of a problem, this improves the quality of the production system.
Some of the limitations are; cost in time and money; implementing these systems takes many years; and during the long years, the substantial loss can occur due to the length process of training employees. Which also makes a significant investment by the company concerning money and the utilization of resources, thus adopting the procedures can be quite expensive and exhausting. Second, is the fear of change, because of increased global competition, many organizations are replacing the traditional approach with these quality improvement methods, however there those employees that resist change due to uncertainties, doubt, and fear from these rapid global changes.
In conclusion, it is hard to separate these two quality improvement initiatives; this is because they revolve around the same objectives, which is reducing defects in the line of production and increasing customer satisfaction. However, due to uncertainty and organization can start implementing the initiatives at the project level, watch its success, and after that implement them in an organization as a whole.
References
An American National Standard ANSI/PMI 99-001-2013. (2013). A Guide To The Project Management Body Of Knowledge (Pmbok Guide) Fifth Edition. Newtown Square, Pennsylvania 19073-3299 USA: Project Management Institute, Inc.
Inman, A. R., & Turner, C. M. (2017, April 28). Continuous Improvement. Retrieved April 28, 2017, From Reference For Business: Http://Www.Referenceforbusiness.Com/Management/Comp-De/Continuous-Improvement.Html
International Atomic Energy Agency. (2006). Management Of Continual Improvement For Facilities And Activities: A Structured Approach. Wagramer Strasse 5 A-1400 Vienna, Austria: The IAEA In Austria.
Pojasek, R. B. (2003). Lean, Six Sigma, And The Systems Approach: Management Initiatives For Process Improvement. Pojasek & Associates, Boston, USA: Wiley Periodicals Inc.
Request Removal
If you are the original author of this essay and no longer wish to have it published on the customtermpaperwriting.org website, please click below to request its removal: