
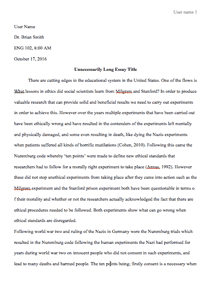
Operations management is concerned with managing resources that are used in direct production of a product or service. Production involves transforming a raw material to a finished product. It is the aim of productivity to produce as many goods and services using the minimum resources. As is the case of Enterprise Rent a car (ERAC) it is a company that provides the services of leasing cars. This company was founded by Jack Taylor after he realized that there is a need for customers who took their cars for maintenance and repair to rent cars.
The input output model consists of inputs being converted to output and getting feedback concerning the quality or standard of the final product.
Â
Feedback
According to this model the input is preparations made to lease the cars and the output is the leasing services. Customers give feedback about the quality of the service.
Ways in which the ERAC can cut costs
ERAC can cut its operations costs and ensure profitability of the company. The different ways it can cut costs include; embracing technology, technology involves use of modern tools, means of communication and using the internet tools. EARC can use the internet as a platform to deliver its services through online business this can reduce costs since there will less offices and workers employed; Through outsourcing, this is the activity of obtaining a product or service from the outside company (Overby, 2007) The services outsourced can the non-critical ones. As a result of ERAC expanding its fleet management services, it has outsourced its vehicle department. It is through outsourcing that EARC has managed to concentrate and put its full resource on management of the company; through telecommunication. Financial resources are used in payment of rent, wages and salaries and other indirect expenses. Communication with the employees and customers can reduce chances of; Go green which means using the natural energies to cut down on the costs. Another way of reducing cost is by forming a collaborative relationship with customers who will ensure customer retention and satisfaction. Employees plays an important part in reduction of costs, EARC employing new workers every time can increase costs by training expenses hence it should also ensure good relation with employees to avoid costs.
Defining quality for ERAC and how control charts can be used to improve quality
Quality can be defined as fitness for use or conformance to specification. According to EARC, maximum customer satisfaction means quality. Control chart are used to show how a process changes overtime. They include;
Six sigma is used to track input output process overtime .the tracked values are used in comparison of the actual results with the expected results.( Gupta, 2015) Six sigma can be used by EARC comparing its expected level of service with the actual or the number of leased cars to the customers over a period of time. Furthermore six sigma can reduce the need for inspection i.e. ERAC will not need to inspect its fleet, monitor the process from the delivery of service and act of the complains of the customers . The results of this analysis are used in decision making. This tracking enables detection of variation.
The time series model, The time series model is used to identify the quality characteristics of a product over time. (Nancy, 2004). ERAC can use time series model in analyzing its performance over a period of time. Time series is used to obtain important data about a service. ERAC uses time series to track its growth like the airport market, the annual rate of revenue. It can help in identifying the suitable areas to improve.
How can ERAC improve its quality using the following tools: flow chart, Pareto analysis and cause effect diagram
ERAC can improve its quality using this tools as follows; A flow chart comprises of steps of a process e.g. when a car leaves ERAC to the time it is returned back by the customers. ERAC can develop a flow chart to ensure all stakeholders have an understanding of the process of service delivery
Pareto analysis is also called the 20/80 rule. This is where 80 percent of the problems in the organization can be caused by the 20 percent cause (Nancy 2004). It can also be applied where 20 percent of the suppliers cause 80 percent quality problems. To avoid these problems AREC should carry out a comprehensive supplier analysis and rationalization and optimization to ensure the best suppliers. Pareto also can show the important factors in the leasing of the car.
Cause effect diagram is also called the Fishbone diagram. This diagram identifies the many causes of an effect and it sorts out the ideas on how to improve quality. ERAC can use the diagram to identify what has caused the quality department in the various departments. It can improve its quality through Fish bones suggested categories; people, processes, procedures and plants.
Â
References
Overby, S. (2007). ABC: an introduction to outsourcing. CIO. com.
Tague, N. R. (2004). Seven basic quality tools. The Quality Toolbox. Milwaukee, Wisconsin: American Society for Quality, 15.
Gupta, D. (2015). Success using lean six sigma in terms of operations and business processes. Anchor Academic Publishing (aapverlag).
Â
Request Removal
If you are the original author of this essay and no longer wish to have it published on the customtermpaperwriting.org website, please click below to request its removal: