
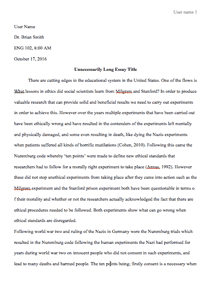
Supply chain management (SCM) is the oversight of information, materials and finances as they move in a process from supplier to manufacture to wholesaler to retailer to consumer. SCM involves incorporating and harmonizing these flows both inside and among companies. The crucial goal of an effective supply chain management system is to lessen inventory. There are seven characteristics of an effective supply chain. An effective supply chain has strong planning capabilities. This means that those businesses that have better planning abilities score higher on the methodology. The supply chain also has aligned metrics, supply chain design, the right material in the organization, enlightened leadership, mature horizontal processes and outside-in processes.
Demand management involves how a business determines what the consumer or the customer wants. The basic element in demand management is demand forecasting which refers to an effort to plan future demand. It can also help in make-to-order and make-to-stock. Customer service attempts to keep customers contented and creates in the customers mind the insight of an organization that is informal to do business. Customer service occurs in four dimensions, that is; dependability, convenience, time and communication. Order management refers to the numerous activities associated with the order cycle which is also referred to as lead time or replenishment cycle. This refers to the time from when a consumer places an order and when the goods and chattels are received. Order management consists of four main parts which include: order processing, order delivery, order picking and assembly, and order transmittal.
There are various reasons for holding inventories which vary from case to case. One need for inventory is for economies of scale in procurement. Holding inventory and buying raw materials in larger lots is economical for a company than purchasing frequent small lots. Another reason is to take advantage of price increase and quantity discounts. Companies tend to buy raw materials in advance and hold stocks if there is a price increase expected in a few months down the line. This makes organizations to buying in bulk and holding records to take advantage of the quantity discounts presented by the dealer. Inventories also help to reduce transit cost and transit times, cater to cyclical and seasonal demand, meet variations in production demand, and to keep long lead and high demand items. Inventory costs are categorized into: ordering costs, carrying costs, cost of replenishment, shortage cost, costs of logistics and cost of loss, pilferage, shrinkage and obsolescence.
Fixed order quantity is the arrangement in which inventory level is continuously monitored and lead time is ordered in stable quantity each time at-hand stock falls to the reorder point. Fixed order interval is defined as a fusion inventory system in which the inventory specialist examines the inventory situation at fixed time period. Economic order quantity is the order quantity of inventory that reduces the overall cost of inventory management.
Economic order quantity (EOQ) is the order of quantity that reduces entire holding and ordering costs for the year. The economic order quantity model is also referred to as economic lot size model. EOQ regulates the optimum order size that decreases total inventory costs. It is a formula for determining the optimal order size that reduces the sum of ordering costs and carrying costs. The formula is derived under restrictive and simplifying assumptions as follows: the order quantity is received at the same time, no shortages are allowed, lead time for the receipts of orders is constant and demand is known with inevitability and does not change over time.
A warehouse is a planned space for the handling and storage of goods and material (Fritz Institute). Warehousing decisions include: reporting which typically focusses on reporting from a single source of truth within an organization. The big challenge of this stage is data integration. Analyzing is the second stage of warehousing decisions. In this stage, decision makers concentrate less on what happened and more on why it happened. Here performance is more important because the information source is used much more interactively. Another stage is predicting. Understanding what will happen in future in the business has vast insinuations for proactively managing the policy for an organization. Operationalizing as a warehousing decision basically means providing access to information for instant decision-making in the field. The last decision is active warehousing. A business automates a business process depending with the role the data warehouse plays in the operational characteristics of decision support.
CASE STUDY 4.2
Ocean Spray Cranberries, Inc. gave a number of reasons for using 3PL for their transportation and logistics area. After looking at the transportation within the logistics chain they realized there was a lot of changeability in this area. The company decided to centralize and bring all of its transportation logistics into consistency while growing into new markets. They looked into cost of expanding the transportation further and the time it would take in order to maintain their main competency. I approve this decision. The company is looking to renovate their transportation but feels this is not the area they outshine their rivals.
According to my understanding I feel that Ocean Spray should consider 3PL based transportation provider which will allow them to develop more systematized transportation operations while still focusing on their primary competency. 3PL based transportation will be able to put more emphasis on the transportation based resources and offer further logistics help.
The first step Ocean Spray should take is to perform a strategic assessment. By doing this the company would become fully conscious of their logistics and supply chain needs and the whole strategy to guide operations. Another step is to make a decision to form a relationship. An external supplier is appropriate because they dont have expertise in logistics and transportation. The company should also evaluate alternatives. This will help them know who they can will work best with. They should also instrument a continuous improvement. This is where the company and its associates start to implement all plans between the companies. The last step is to structure an operating model that will help form and withstand relationships.
The most suitable relationship would be strategic alliance because the company is in a competitive juice industry. They should be able to do better than their competitors. They will also want to be involved to ensure everything is delivered in time and in an acceptable quality to keep their consumers pleased. By being involved, Ocean Spray will also advance knowledge in supply chains and logistics.
REFERENCES:
Bill, M. (2014). Planning Safety Stock Levels: By Quality or Time?
Brobst, S. and Rarey, J. (2003). Five Stages of Data Warehouse Decision Support Evaluation.
Olsen, D. R. (2003). Gower Handbook of Supply Chain Management.
Request Removal
If you are the original author of this essay and no longer wish to have it published on the customtermpaperwriting.org website, please click below to request its removal: