
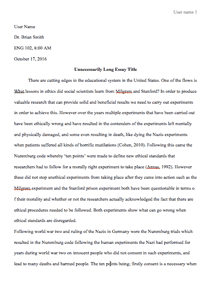
Dropex Limited is manufacturing and marketing firm in the UK. The main products by this company include, breakfast cereal, nutritional foods and other foods for the entire family. Its main customers include malls, supermarkets and similar convenience stores which sell the products either in wholesale or retail, and individual customers (Goetsch and Davis 2014). The Organisations products have been tested and duly certified by the various bureaus of standards institutions as fit for consumption by the whole family. All their products bear upon their packaging, the requisite industry marks of certification. In fact, it has been rated by the industry as the home of healthy foods.
Dropex is very keen on its reputation, branding and intellectual property rights. Towards this end, it has registered trademarks over all the brands and product names that it has developed over time. This deters product infringement by competitors. Further, all its products have a distinguishing packaging that sets them apart from those of its competitors. By so doing, the Organisations products are clearly distinguishable. The organization uses cost-based pricing method to price their commodities. This means they only consider overhead and other costs incurred in carrying out the whole process, and an additional mark-up price that translates to their profits (Stanton, Gough, Ballardie, Bartram, Bamber and Sohal 2014). This pricing method ensures unexpected cost changes have been catered for and is favourable to customers. By selling cheaper products, it is an added advantage to the organization as it is able to curb competition from others in the same industry. Offering quality products is one of the core values of the organization.
The following benchmarking diagram aids in showing the above order qualifiers and order winners At Dropex Limited.
Responsiveness
Reliability Pricing
Quality
Responsiveness
efficiency Branding
Pricing
Agile Supply
Lean Supply Order Qualifier Order Winner
Lean Benchmarking Diagram
Lean supply focuses mainly on value adding and waste elimination while agile supplies focuses on a wait-and-see approach in offering products.
Problem Identification
One of the major challenges facing this organization is delays from their suppliers. The company has been using middlemen who would acquire raw material such as agricultural products from farmers and supply to the organization in bulk. Delays in supply of materials is a major hindrance to fast and efficient manufacturing of products in organizations hence a drawback to the manufacturing process since they lead to an increase in the manufacturing time of the company (Fullerton, Kennedy and Widener 2014). At Dropex Limited, Some of the commodities such as cereals for weaning babies were not readily available on some days. Effect of delayed supplies could be felt in the final productivity rate of the organization.
Delayed supplies are evident at Dropex as the number of customer complaints have increase because of the inconveniences caused by the shortage. The drastic reduction in the amount of revenue collected on some days due to lack of some of their completive products also clearly elaborates how the impact of delayed supplies is felt at Dropex. The number of clients pulling off from contracts previously entered by the company also portrays the problem being faced by the organization.
Other problems facing the organisation include one of the organisations main customers, The Tauriah Mall, faced liquidity problems and subsequently became insolvent (Fullerton, Kennedy and Widener 2014). As the mall is usually supplied on credit, this has meant a shortfall of expected funds for the Organisation. Moreover, one of the Organizations banks has gone under and is under receivership. Consequently, the Organizations funds held at the bank are subject to the receivership proceedings. It is imperative for Dropex to take measures that will curb this shortfall.
Effects of Supply Delays to the Organization
The delays cause shortage to some of the companys products on some days. This shortfall essentially leads to the loss of some potential and loyal customers. When products are not at the disposal of customers, some of them abandon the organization for another (Fullerton, Kennedy, and Widener 2014). Reduced sales translate to reduced profit margins and this poses a serious drawback to Dropex Limited as they are not able to maximize on profits yet it is one of their financial goals. An uninterrupted flow customers is vital to the existence of any organization.
Reduction in profits at Dropex Limited leads to stagnated growth. With less revenue being generated by the firm, the workers are not well paid and this can reduce employee morale and productivity. These delays also harm the organization as it becomes a window of opportunity for their competitors. The organizations reputation and image have been distorted during the periods that they incur shortages since there is the domino effect caused by delays in supply of materials by vendors and suppliers. In relation to the other problems facing Dropex Limited, the organization suffers a shortfall and is not capable of fully meeting its financial obligations to its main suppliers while at the same time keeping up with its usual operational costs. Further, as a result of the shortfall, the Organizations credit score has suffered thus reducing the available avenues for capital injections
Literature Review
Lean management system has its roots in the manufacturing industry, more so at the Toyota Motor Corporation where it embodies production of only what is necessary, when it is required, with the right quantity needed (Martinez-Jurado and Moyano-Fuentes 2014). Actually, the lean management system has come to be synonymous with the Toyota Production System. Lean management approach is a practise where organizations strive to ensure positive co-relations exists in cost reduction, time reduction measures and improvement in quality and other related processes. Various business processes within an organization are identified and those that are not of value creation eliminated (Martinez-Jurado and Moyano-Fuentes 2014). This ensures incremental improvements in an organisation.
Principles of Lean Management
Various principles guide the lean management implementation process in any organization. These principles, according to Khalili, Ismail and Karim (2017) include:
Identification of value of the products from the customers stand point.
Identification and elimination steps that are not of value creation in the business process.
Ensuring that the flow of value is seamless to customers.
Allowing customers to pull value from subsequent upstream activity in organization.
A critical analysis of the systems so as to achieve perfection and continuous improvements.
This lean management concept is alive in organizations due to the fact that productivity potential of an organization is inhibited by innumerable forms of wastages in the business process. The various types of wastages that can be alleviated by lean management systems include:
Overproduction of components, neither intended for immediate sale nor for stock. This results to incurring extra expenses that could be avoided in the meantime.
Unnecessary transportation of materials.
Waiting periods during productions. These periods could be due to lack of a smooth work flow and proper planning of how work will be carried out in the organization.
Defects and spoilage of products hence rejection by clients. This could be as a result of producing low quality products hence clients not willing to purchase
Holding of excess and unneeded inventory. Materials to be used at some later date could be purchased in advance, for example, due to the fear of increase in prices of raw materials. This leads to holding unnecessary inventory.
Over-processing. Putting more than what customers are willing to pay for products. Customers believe in having value for their money. Therefore, most of them will purchase only what is essential and the features they desire to have in the products. If a firm does not conduct market analysis prior to introducing a product, they may end up not having ready clients for the added features in their products.
These wastes are evident in many organizations especially those in the manufacturing sector. For efficiency purposes and maximizing on output, the lean management should be put in place so as to ensure both financial and non-financial goals of the organization are met.
Biazzo, Panizzolo and de Crescenzo (2016) suggest that many organizations are taking up lean management so as to eliminate wastage in the product innovation and development process. Lean innovation is the process of applying lean management in the manufacturing concept (Kumar 2013). In order to improve the operational processes of a firm, it will be imperative to integrate the lean innovation practices with that of the management. In the innovation process pyramid, lean management lies at level three of the pyramid and it spreads across various departments in the organization (Myerson 2012). Constant search for ways of eliminating waste is carried out throughout the organization, for example in product design, since its output has direct impact on product performance. Generally, lean approach is applied so as to increase benefits gained from implementation of the lean principles in the production process. This is through the creation of products that are of value addition to customers and have a low rate of wastage.
In the recent years, there has been rapidly changing organization environment for organizations and this, according to Bhasin (2015), has resulted in the need for structuring the organization so as to ensure continuity of improvement in its performance. Organizations use lean thinking so as to improve efficiency, quality and reduce on customer response time (Kumar 2013). Strategies adopted by firms are more holistic other than activity isolation operations. Lean practices should be integrated across all business functions. Lean practices are seen to have a positive impact on different organizations performance. This conclusion was arrived at from a research of the Management Accounting practices in relation to lean management (Myerson 2012). Lean management accounting practice avails financial controls that intergrade with operations to achieve desired benefits.
A lean organization focuses on customer value and the processes for its continuous improvements. Its ultimate goal is to provide perfect value for customers and ensure zero wastage. Wastes are eliminated along value streams and not at isolated stages within an organization. A lean organization uses less effort, human resource, time and capital in carrying out its operations (Fullerton 2014). These lead the appropriate response to customers desires through production of high quality products.
Operational Benefits
An organization that practices lean management accrues various benefits in both the long and short run. Dropex would enjoy various benefits as a result of implementing lean management systems. Some of the benefits would include:
Improved quality. Lean management activities gears towards quality improvement. Root causes for problems are identified and solved on time. Quality is also improved through employment of competent workers and ensuring raw materials purchased meet qualifying standards (Bhasin 2015). Cereal and other food products manufactured by Dropex should be duly tested ensuring quality production. This w...
Request Removal
If you are the original author of this essay and no longer wish to have it published on the customtermpaperwriting.org website, please click below to request its removal: