
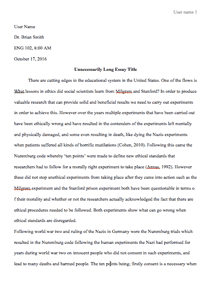
Lean Manufacturing can be defined as an operational approach which works towards the accomplishment of shortest possible cycle time through the use of waste eradication philosophy. This method has been derived from the famous Toyota Production System(TPS) the main concern is to achieve an increased value ability in the elimination of waste products as well as supplementary reduction of work. The system works by decreasing the gap between customer order and delivery. The system is designed for productivity enhancement, customer satisfaction, employee morale and last but not least production time output. The benefits seen comprise of lower production costs, higher quality in production, and also short periods. Lean manufacturing as a model, represents half of the human effort in business organization, compact investments in tools and equipment, engineering and maintenance of production hours.
Food Manufacturing in the UK Using Lean Principles
The key objective of UK food manufacturing industry is to achieve high economic development levels. The upgrading in productivity has recently become one of the main concern in the food industry so as it can take up a competitive gain in the global market. The main problem facing UK food industry is discovering the wastes and meeting the market price while maintaining the generated profit. The only way out is to reduce the expenses on production. This article discusses how production principles of lean manufacturing can be used in food production to increase the efficiency of production as well as the quality of products manufactured. The main aim of Lean manufacturing is to assist employees in the food industry create more improvements in food production. It ensures that precise development mechanism is implemented for compelling reasons, clearly without forfeiting quality or food security. The system offers a fresh and current perspective on effective methods of production, it identifies mechanisms to reduced company breakdowns, reduced quality liability, enhanced joint efforts and increased profits. It focuses mainly on food company business management and current development processes.
Methodology
A Lean board was established with various workers from different sections in the company, who were conversant and knowledgeable about the processes, products, the nature of the equipment used, and management mechanisms. The team leader collected the company production data and generated the production plan by exploring each stage of the manufacturing development with support from other company workers. Tactical areas for executing lean tools were branded in based on the statistics and observations made. Among several concerns associated with food manufacturing, colossal wastes in raw materials increased water usage, liquid nitrogen and electricity, lack overall maintenance in production, the breakdown of the machine during the changeover and also the lack of effective communications between the industry departments were considered during the investigation.
Five lean principles were identified: Quality, Delivery, Cost, and Safety Volume on the consumers and Morale. Lean projects were powerfully pertinent to the company as they were carefully and methodically selected and implemented to attain substantial instant benefits with barely minimum investment. Various data collection procedures and planned problem-solving methods were also identified. Different company boards were displayed on the company floor to correspond to the action lists as well as control charts. The development of lean implementation techniques was regularly reviewed in leading organization conference as well.
Results of Lean Implementation
Despite the application of different lean techniques in food production the packaging, production and warehouse areas results were recorded based mainly on four lean principles; Overall Equipment Effectiveness, quality, Single Minute Exchange of Dies and Waste Reduction.
Statistics on waste reduction
The data collection on food production over a three-month period showed that frying, forming, amalgamation, X-ray, and crumbling activities represented high rates on company wastes. The wastes were frequently generated in the production processes compared to other areas in production. With the application of lean principles the daily wastes produced in amalgamation, raw materials when weighing, freezing and packing areas were radically reduced. The figure below shows statistics on waste Reduction in UK food manufacturing industry.
As a section of lean implementation, the board concentrated on effective strategies for reducing the amount of time used in the production of food. The employees required to leave the manufacturing section to collect raw materials for food preparation. Though, the employees were not given the guarantee to re-enter production devoid of cleaning the production equipment this is done to make sure that no noxious wastes enter during the manufacturing process. This means that employees have to maintain high levels of hygiene before entering into food manufacturing section again as the cleaning station is close to the production entrance hall. As a way out to get rid of this waste of action, a new sanitation station was established adjacent to the production exit so that staff does not carry any contamination to the production secretion as a result higher production efficiency is achieved.
Conclusion
This report shows that it is possible to use the Lean technique in food manufacturing company to improve the levels of production. Systematic implementation of lean tools efficiently helps in waste elimination in different steps regarding the production cycle across different ranges of manufactured foods. The establishment of lean principles across the entire industry inclusive of the management area resulted to effective well structured, clean and safer production mechanisms with increased productivity arising from motivated workers as well as reduced duration in searching food manufacturing equipment. The Single-Minute Exchange of Dies under Lean technique activities have improved the opportunities for establishment time reduction thus leading to rapid food production as well as shorter lead period. The implementation of the Lean technique in food production has also provided an opening to measure Overall equipment effectiveness; this results into more competent industrialized mechanisms. In brief, the activities of lean can smoothen and improve the development of the food company to be highly competitive in the market by reduction of food production cost, enhancing teamwork efficiency, improving the consistency levels of manufactured products and improving the standards of productivity.
Request Removal
If you are the original author of this essay and no longer wish to have it published on the customtermpaperwriting.org website, please click below to request its removal: