
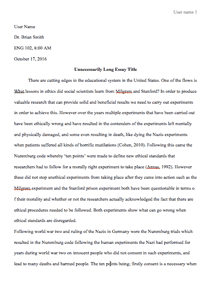
Stiff competition in the world of production has challenged many business entities to invest in sound logistics, supply and chain management to sustain their returns. To this end, the recent motor vehicle production expansion across the globe has seen the reacquisition of companies, mergers, and reinvention of others to suit and match the ever-changing trends of technology in the industry as well as respond to the needs of dynamic customers. As such, a corresponding need for the development of efficient mechanisms through which manufactured vehicles transported from one place to the next has become a vital necessity. Supply chain management does not begin when a given entity orders a product from its accustomed supplier. Rather, it is a series of activities that precede the delivery of a product to the final entity that utilizes for delivery to the final consumer. Hugo (2003) describes logistics and supply chain management as the coordination of production of goods and transport among the players in a supply chain to realize the best mix of returns (p. 4). Supply chain management entails the coordination of all supply chain activities, starting with receipt of raw materials and ending with a satisfied final consumer (Heizer, Munson & Render 2017 p.441). This paper explores operation, supply chain management, specifically quality management and logistics at Mercedes and issues faced by the supply chain managers of Mercedes.
Company Overview
This is a multinational subsidiary of the Daimler AG; a Germany manufacturer brand that is used for the luxury buses, automobiles, coaches, and trucks with headquarters in Stuttgart, Germany. Its origin is traced to Gottlieb Daimler and Karl Benz who created the first petrol car in 1886, and, Wilhelm Maybach. It is ranked as one of the best vehicle production companies in the globe; it is the number10 among the leading company brands in the world (Intrabrand.com, 2014).
The Daimler group not only aims at providing the best services for her customers, but also, value and high notch premium customer quality. It has more than 14 subsidiaries worldwide producing luxury cars, buses, trucks, vans, and financial matters. Furthermore, as a result of its strategy of offering the best quality, it has over 100 vehicle models in more than 200 countries, demonstrating the resolve to provide the best brands worldwide. Available data shows that 1.565,563 million Mercedes-Benzes were sold in 2013. The organization boasts of more than 274,000 employees worldwide (Daimler 2013). Mercedes primarily engages in the production, distribution, and selling of its products against its renowned core competitors like Toyota, Volkswagen, BMW, and General Motors. Consequently, the Mercedes Company has incorporated various strategies into its key operations including quality management, transport and network thus improving service delivery.
Quality Management between Mercedes and Toyota Companies
Heizer et al. 2017, post that quality management is the set of activities that aim at creating value in goods and services by transforming inputs into top-notch quality outputs (p. 213). In addition to that, quality management entails offering of fast, affordable, accurate, dependable and on time services while logistics, transport, and channels entail ensuring a flawless design by manufacturers; quick delivery and a seamless transport aimed at attaining internal perfection (Davila, 2010).
Quality management has been a driving force in the automobile industries and has been considered as one of the major organizational functions that are entrenched within the decision-making process, prioritizing of functions, resource allocation and service delivery (Bilich & Neto 2000 p.5). Moreover, for a company to stay relevant in the contemporary competitive business world, quality management must be established and practiced at every level. Interestingly, the Mercedes Companys core values rely on quality, reliability, and safety. Nonetheless, it is common knowledge that it maintains a reputation for high durability and quality in the marketplace. For example, due to the companys exemplary quality, it achieved 5th position overtaking Toyota for his car models. Also, in 2008 Mercedes received an award (the Platinum Plant Quality) for its exemplarity in the auto industry (Bogue 2008). Further, it has a reputable brand thus cutting a niche in the marketplace which is an envy of its competitors (Jackson 2001). However, change in production led to the company shifting from its core strategies to technology and innovation. As a consequence, a shift of consumer base occurred, bringing to the fore a negative element in quality management strategies.
On the other hand, Toyota Company has been seen as the pioneer of quality management with a continuous improvement thus bringing about extra value to the customers. It based its quality management on kaizen or quality first aimed at total participation and constant improvement which drawls input from all employees. In line with this, it introduced the Toyota Way which combined the kaizen principles to minimize overproduction and waste, and, freedom of expression from employees by providing a favorable bureaucratic environment (Bid.org 2013). Despite that, Toyota saw its valuation drop in the world market due to the massive recalls of some of their cars and these plagued the industry (Rodionova 2016). Through the analysis of the quality management strategy of the two organizations, it is paramount to stress that for maximum rewards or benefits to be realized; quality management must be entrenched with the external and internal processes, facilities and resources (Djerdjour & Patel 2010 p. 33-34).
Channels, Networks, and Transport
Channels, networks, and transport can be logically intertwined with logistics, supply chain management which is the movement of materials and products to the proper place and in required quantities (AIMS Education-UK 2016). The Mercedes Company aims at reducing logistics expenses by about 20% per a vehicle as they have invested a lot of Euros to reorganize the supply chain network. Also, it has introduced a consolidated center in Speyer, where European suppliers repackage all components for efficient shipping to U.S, South Africa, and China. It builds cars in 26 different countries with partners like Renault, Valmet, and Magna Steyr. Also, with the latest information technology like real-time radio-based signals, it has developed intelligent networking plants that will boost productivity and profits (Hetze, 2015).
On the other hand, Toyota has three policies- Fair policy, mutual trust benefit and contribution to the local economy. Fair policy entails considering the poor whereas mutual trust is a belief of building a long-term relationship through mutual trust while contributing to the locals. Such policy is aimed at globalizing its operations by purchasing materials and parts from the local suppliers. All these are based on continuous improvement (Bid.org, 2013).
Theories
There are various theories that are applied to supply chain management. Conversely, two theories are discussed herein, and they are; Theory of Constraints (TOC) and Agency Theory (AT). Theory of Constraints presupposes that planning of activities, controlling and execution must be done or performed through constraint management paradigm by continuous improvement methodology. For maximization of profits, one should identify and act on the constraint thus avoiding the system and reaching the target- system profitability and profits. Theory of constraints assists and helps the supply chain managers in identifying and creating a win-win solutions or conditions between the systems entities. TOC uses continuous improvement methodologys five steps meant to identify constraints and exploit them; subordinating everything to prior decisions; elevating the systems constraints, and, getting back to step one while not allowing inertia as the constraint in the system (don Santos, Marins, Alves & Moellmann, 2010).
Furthermore, the approach of TOC has a nemesis- Drum-Buffer-Rop (DBR) or synchronous manufacture (Gaither and Frazier, 1999). Also, Drum-Buffer-Rop forms the basis through which TOC is applied to production while being flexible in the inventory minimization. Therefore, it can be explained: Drum which has same analogy like the drums that define the military matches; likewise in TOC, the drum is the constrained resource which sets the base for the entire production system, as a supportive component for the TOC third step (Goldratt & Cox III, 1992); Buffer is the safety time representation for constrained resource protection, which keeps constraint flow in case there is a problem, and puts the work in constraint resource at risk. However, there is a likelihood of creating a secondary buffer during the process. Lastly, Rope synchronizes materials arrival on the buffer and admits them to the system.
In line with this theory, it applies to the production and management of the Mercedes Company. Managers use this theory to synchronize their production units. For example, the formation of a consolidated center in Speyer, where all components are repackaged by European suppliers for efficient shipping is aimed at reducing production costs, creating and consolidating its resources. Also, through constant reconfiguration of their logistics, the company has elaborated the client focus, and as a result, customers can now get fast delivery of the S class without delay unlike before. The implementation of such plan is meant to reduce lead time on sequence manufacturing thus customers can change their orders hence the removal of pearl chain (Hetzne, 2015). Likewise, the Toyota Company uses lean production consisting of continuous flow process, leveling of workloads and pull system- 3 building blocks. As a framework for constraint management, Toyota uses CS to maximize system goals or throughput accomplishment.The creation of hybrid cars and use of Kaizen principle entails satisfying the customers, the employees while making a profit thus a win-win situation for both parties.
Agency Theory
Agency theory has been popular in law, finance and economics, literature, and, it focuses on organizational stakeholder divergent goals and interests, and how employee compensation can align them (Eisenhardt 1989; Fame & Jensen, 1983). Unlike days when there were no job specialization or chain management, control or ownership management is separate in the modern world of corporations. However, with the removal of stockholders from the daily operations of companies, agency costs arise. Examples may include the extravagancy management. For, instance, hiring a jet for the companys managing director; or increasing the managers prestige. All these do not add any value to the company but an individual, and it is detrimental to the company. Besides, shareholders and managers may differ on priorities for the company thus leading to agency costs whereby shareholders can easily diversify risks as compared to managers who may incur little risk through their salaries- more emphasis on salary increment and low interest on uncertain incentives. This is the scenario in companies controlled by managers.
On the other hand, agency theory plays a critical role in the analysis of manager-employee relationships: non-managers compensation design. On this front, interest divergence exists between the manager (principals) and the employees who take the role of agents. The main question to ask in such a scenario is how to minimize agent costs. The theory proposes that the principal must choose a scheme that is favorable to both of them; aligns their interest together thus reducing agency costs. The contracts can either be outcome-oriented or behavior-oriented...
Request Removal
If you are the original author of this essay and no longer wish to have it published on the customtermpaperwriting.org website, please click below to request its removal: