
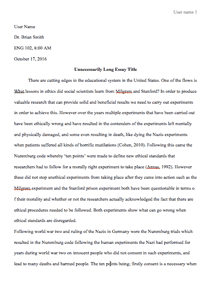
Riveting is the priceless and old technological invention. It is dated back to Bronze age. Riveting is the process and method of manually or mechanically joining two parts together using special metals called rivets. This technology is widely employed automobile industry. Parts of car, plane, boats, and home equipment among others are securely joined and connected using rivets. Poor joint quality has caused accidents and subsequent loss of lives. For instance, riveted parts of plane that cannot tolerate stress and corrosion have caused several plane crashes. The quality of the joint, accuracy, strength depends on the mainly on the tools used to position, drilled rivet holes and fasten. Also, for mass production and reduction of cost, riveting tools fixtures are used. This paper discussed the vital features of fixtures, central principles of design of fasteners, materials used, challenges faced by manufacturing companies. It also focused of advantages and disadvantages of riveters.
What is riveting tool fixtures?
These are machines that are used to hold, locate and support parts for the purpose of riveting operations. These are technological production tools designed and developed for accurate manufacturing of similar parts. These parts can be interchanged. They aid in assembling of mass number of identical and interchangeable components. Examples of riveting tools includes: customized riveters, special arms, compensators and feeding devices for rivets. Fixtures are clamped to the working place. Examples of the riveters are: first, there are customized fixtures. There are two types: positioning and movable fixtures. The former is used for positive alignment. They hold the one or more pieces in place during riveting process while the latter is movable and are effective. They can support single machine to installed rivets in part of a piece. Secondly, rivets feeding devices. These are fixtures that are used to feed rivets or parts to riveter for quick mass production. Systems to deliver parts either via tubes or slides can be incorporated into fixture. Moreover, compensators are used by riveters to cater for difference thickness of work piece.
There are several riveting tool fixtures manufacturing companies across world. Their products vary depending on standards, customer requirements and product specifications. There are different materials used to make fixtures. These include:
Carbon steel. This is use for making standard tools for cutting parts.
High speed steel used for making drills for rivet holes.
Collet steels. Also, die steel used in press tools.
High tensile steel is used in making fasteners.
Nickel chrome. Steel used for making gears.
Casted iron. Cast iron has self-induced lubricating features and can tolerate vibrations. It is used for making odd shapes specific to machines.
Fiber and Nylon. They are soft and slippery. Used for lining of clamps to reduce damage due to pressure.
Phospher bronze. It is strong and thus, used for making nuts.
Shrinking free steels. Materials with high degree of chrome or carbon, ability to withstand distortion due to heat. Such materials were used for making press tools.
There are essential characteristics of riveting tool fixtures manufacturers and users consider. These features includes: first, minimum idle time. In this regard, fixtures and riveters should be easy to clamp, position and unload. Secondly, easy replacement and repair of the parts. Fixtures should have standards spare parts by all means so that repair and interchangeability is possible. Thirdly, riveter should be coolant enabled so that efficiency is maximized. Fourth, hardened surfaces. Supporting and location surfaces should be manufactured using hard materials. This will ensure accuracy and durability of the tool. In addition, tools fitted with pads. Faces of the fixtures contacting the finished product or surfaces should have pads to minimize damage and spoil. Also, safety of the tool. The fixture should be safe to the user and environment. Ease of use is another factor. Fixture and its parts should be portable, consistent and safe to carry around. Importantly, the cost of designing and manufacturing fixture should be sound without sacrificing the quality of the tool. Finally, fixtures have to ease of ejecting after work is done. Essentials tools for ejecting riveter from the work piece should be installed.
Key Principles of Riveting Tools Fixture Design and Manufacture
The following are the central principles of designed and manufacture of fixtures.
First, consistency of the fixture. Design of fixtures should ensure accurate and same results. Rivets should not be inserted in different location but on the correct location of the work piece. Secondly, reduction of the idle time. The design of the fixture should enable the loading, moving and ejecting takes the lease time possible. It should not delay the process of its usage. Thirdly, portability of the fixture should be considered. Fixture should be of light weight, small in size and user friendly for easy manipulation. Fourthly, hardened and coded materials should be used for making part of the fixture. In this regard, fixture will ensure accuracy; avoid wear and tear and frequent repair and maintenance. Also, corrosion of the machine will be reduced. As a result, there is reduction if cost of repair and maintenance. Morever, accurate positioning. The locating devices should be incorporated to ease the work. Loading and unloading of the pieces to be worked on should be easy and quick. This will reduced the time wasted on loading and positioning of the work piece.
Factors Considered When Designing and Manufacture of Fixtures
There are essential factors to be considered by manufacturers for design of riveting tool fixtures. These includes:
Safety of the machine. The parts of the fixture should be safe to the operator and environment. Also, it should ensure safe operation. It should not damage or spoil the work piece.
The cost. The cost of designing and production should be as economical as possible. No extra cost should be invested by the customer or manufacturer.
Capacity of the fixture. Fixture should hold considerable number of pieces. Clearance of the machine to allow for movements and clearance.
Manipulation arrangements. Fixtures should have enough space for loading and unloading. Thus, operation is easier and quick. it should accept different sizes of work piece.
Location is another factor. Movement of pieces should be avoided. No sharp corners. The location should be consistent. Locating devices should be wear and tear resistant, hardened and of high accuracy.
Production requirements. The main purpose of designing and manufacturing of fixture for mass production of components. The right components for specific production should be considered.
Holding and clamping. Fast fitting clamps should be used. The process should be safer to the work piece.
Devices for pushing and ejecting fixtures. Tools to ease in ejecting fixtures from the work piece should be riveted on the machine. This will save time and ease the operation.
Advantages of Riveting Tool Fixtures
High and mass productivity. Fixtures increases easy, quick, accurate production of joints by eliminating manual locating, marking and checking. Time wasted on position and operation is reduced because of high speed of drilling, riveting and fixing.
Minimal skills. The use of riveting tools does not require special skills to be acquired. It can be operated by semi-skilled and untrained operators. This reduces the cost of employing professionals.
Interchangeability and quality. Riveters promote production of pieces of recommendable accuracy, duplicates and interchangeable in large numbers.
Reduced production cost. The cost of production, simple and ease of assembling parts reduce the general unit cost.
Disadvantages of Riveting Tool Fixtures
High cost of design and manufacturing. Manufacturer and experts of riveting fixtures incurred a lot of production cost due to changing technologies, market demands and standards.
Constant changing customers demand. Customers required special tools for fastening rivets of varied sizes. Big and non-standard rivets present a challenge to the existing fixtures and called for redesign and production of other tools.
Changing technology. The invention of varying thickness materials, fragile and delicate materials, require development of appropriate fasteners. For instance, installing lens on medical tools using rivets, required the used of gentle fasteners to avoid damages and spoils. That was and added challenge to manufacturers and designers of fixtures.
The fear of future changes. Experts, designers and manufacturers feared the change in technology could affect the adaptability of the fixture. Customers required fasteners that would remained relevant, usable and adaptable to future changes.
Challenges of Riveting Tool Fixtures
First, the evolving demands. According to Robert Schoenberger, riveters manufacturing are facing dynamic customers and market demands and are working hard to meet those requirements. This is a challenge and an extra cost for these companies. In this regard, unique customers expectations also present challenges to experts and manufacturers. Continued revolution in rivets technology also challenges the manufacturers of riveters. This is because high-tech rivets cause harm to work piece if used with existing rivets drivers.
Secondly, technological change challenges manufacturers. The demand of light weight automotive calls for the use of lightweight materials such as materials. In this regard, new fastening tools should be design and manufactured. This challenges manufacturers to invest more on design and production.
Thirdly, fixing of delicate and fragile parts such as lens and glasses to other hardened components requires the use special fasteners. This was challenge to manufacturers of fixtures. For instance, manufacture of surgeons protective gear. It had delicate and fragile plastic lenses that required careful and gentle fixtures to avoid damage when installing and repairing. Manufacturers had to design special fasteners. Orbiform design orbital riveting machine design a special gentle fastener (John, 2007). This was added extra production cost.
Fourthly, crowded and complexity of the planes and aircraft makes riveting hard. Drilling and fixing of the parts by robots made is difficult. Redesign of robots and development of software is expensive (Dakdouk D. and Fengfeng)
Furthermore, different rivets size and standards. The use of different rivets with the existing incompatible fasteners was a great challenge in the robotic and automobile manufacturers. They had to redesign and manufacture their fasteners. That increased production cost. For instance, Edward of Honda Engineering, programming robots to recognize different position on the work piece was easier, but differences in head of rivets was a challenge.
In addition, the fear of adaptability of the fastening technology. Most fixture manufacturing and customers fear constant change in technology. The adoption of some fastening tools specified for some materials could not be used in other materials. If technology continues changes, plans for the future need to be in place (Edwards). That added an extra speculation and manufacturing cost.
The General Principles of Designing Riveting Tool Fixture
The following were the general principles governing the design of fixtures.
First rule to consider was making fixture and fastener consistent. The output of the same process and tools should be the same always. It should not produce different results. Secondly, decision on locating and positioning of binding and position devices. Locating devices should be accurate and consi...
Request Removal
If you are the original author of this essay and no longer wish to have it published on the customtermpaperwriting.org website, please click below to request its removal: