
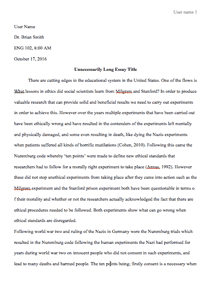
The modern construction industry exists and operates in an environment that is not only economically and technologically dynamic but also politically vibrant. The continuous advancements in technology have far reaching effects on the construction industry (Li et. al., 2009). Today, most of the construction projects appear to be more complex than ever before. This complexity aspect makes calls for proper resource allocation, effective planning and control in order to ensure that the entire process runs smoothly, on time and operates within the projected budget (Haroun, Loghman, & Mahmoud, 2012). Resource allocation is a diverse concept whose proper understanding plays a critical role in the achievement of the firms set goals. The entire concept refers to the process of assigning as well as managing organizational assets in a way that supports its strategic goals (Pan & Goodier, 2012; Rajeevan & Nagavinothini, 2015).
For instance, resource allocation encompasses effective management of tangible organizational assets such as hardware to make the most appropriate utilization of the firms softer assets such as human capital (Kanda, 2011; Sakka& El-Sayegh, 2007). Similarly, effective completion of a given construction project calls for the appropriate judicious scheduling and allocation of the available resources. Most of the resources used in construction projects include human resources, equipment, and building materials. The availability and supply of these resources are affected by some critical variables such as labor disputes, seasonal shortages, competing demands, the breakdown of equipment, delayed deliveries, and a plethora of interrelated uncertainties (Salunkhe & Patil, 2014; Daniel & Guide, 2010).
Comparatively, sequence optimization plays a critical role in ensuring that the goals of a project are achieved as planned (Riedmiller & R i e d m i ll e r, 2011). This concept allows the person in control of the project resources and processes to align the project processes and operations regarding the manner and the structure they were planned to take place. Sequencing optimization can help in reducing the time set up for a project by ensuring that similar and related products are produced one after another(Pan & Goodier, 2012). Also, the project manager mainly the engineer in control can adjust the set sequence manually after the automatic sequence optimization.
In summary, resource allocation and sequencing optimization are two critical processes that initiate and ensure that success is achieved when executing a project in the off-site construction industry (Barlow & Ozaki, 2016; Shen, Wang, &Hao, 2006).This paper aims to provide a detailed literature review covering the off-site construction industry, its differences, and similarities to traditional manufacturing, resource allocation and sequencing in production and different optimization techniques.
Off-Site, Modular, and Traditional Construction
According to Sorrentino (2013), OSC refers to effective planning, design, fabrication, and assembling of different essential building materials at a different location as opposed to their final site of installation. This process is mainly carried out to back up the rapid and efficient construction of a permanent structure. In most case, these building materials are primarily fabricated in a particular location before being transferred to their final destination for use (Lorterapong, 2014). The entire concept of OSC is often characterized by a unique supply chain optimization strategy and an integrated planning technique.
Besides OSC includes a variety of building materials, digital software, scales and systems, different manufacturing and fabrication techniques, and a range of innovations in social and technological integration (Riedmiller & R i e d m i ll e r, 2011). These materials are considered as the essential inputs required for one to complete a project using the concept of OSC. Different componentized and modularized elements utilized in the structural, enclosure and interior partition are considered as the outputs obtained from the OSC project. The optimizing strategy used during OSC entails effective integration of these components and supply chain through continuous and sustainable research, design, testing as well as prototyping (Haroun, Loghman, & Mahmoud, 2012).
On the other hand, the concept of Modular construction stands in between offsite and traditional concepts of development (Schaffer, Caruana, Eshelman & Das, 2009; Landry, Malouin, & Oral, 2013). Modular construction represents a complete concept of construction in factory finish up due to the ability of its products being shipped and assembled as three-dimensional volumetric units. Most of these units are often structural or service units to be joined at their destined locations. Modular construction is made up of two different segments: permanent and relocatable modular. The re-locatable design is sometimes referred to as temporary modular and comprises of different structures that meet temporary space demands and can be purchased immediately or leased in a short-term agreement (Stanczak, Wiczanowski, &Boche, 2016).
Examples of temporary modular buildings include communication pods, job site trailers, show rooms and temporary classrooms (Landry, Malouin, & Oral, 2013). Conversely, permanent modular construction is still an evolving concept with limited popularity in a plethora of developed countries. This concept is commonly used in government buildings including schools, hotels, healthcare facilities, and a multitude of buildings put up using the traditional on-site construction techniques. The modular industry comprises of manufacturers, direct manufacturers as well as dealers (Landry, Malouin, & Oral, 2013). In this case, manufacturers may produce different modules to serve general contractors through direct arrangements or by use of dealers assigned to a particular company.
According to Lorterapong (2014), the inside-out approach to building is one of the most common construction technique used in modular manufacturing. The process entails construction of modular frames as planes which are consequently fitted as frames and completed later from inside out. For instance, the building of a school dormitory unit may take a frame sequence entailing the design of the interior surface, electrical and power fitting, plumbing and fitting of water pipes, and cladding. This approach helps the contractor to evade constant interruptions that are commonly experienced in on-site construction.
Salunkhe and Patil (2014) argue that traditional construction is sometimes referred to as on-site construction and often used to describe different types of linear construction. On-site construction entails full completion of all construction steps of a project must be completed at the primary construction site before moving on to the next phase. Traditional construction occurs in a typical linear format and ignores whether issues such as damage and inconsistent availability of labour can impact the quality of the building (Stanczak, Wiczanowski, &Boche, 2016). The entire schedule and planning of the activities to take place when using the traditional technique rely on weather conditions since all construction occurs on site.
Similarities and Differences between Offsite and Traditional Construction
Striking similarities and differences exist when using traditional on-site and off-site construction techniques.
Differences
First off-site construction is a unique process that utilizes prefabricated construction elements and building materials assembled in a particular factory before being transported to the final destination entirely or in most cases complete (Stanczak, Wiczanowski, &Boche, 2016). However, traditional construction in which primary building elements is constructed mostly or entirely at the site. Secondly, off-site construction brings in to play a simultaneous interaction of activities occurring at a 50% efficiency rate while onsite construction is a typical form of linear construction which requires every step to be accomplished before moving to the next phase (Schwindt, 2005).
Thirdly, it is easier for the manufacturer and the contractor to have a consistent and a quality-controlled manufacturing process in off-site construction, as opposed to the traditional technique quality of the building, is impacted negatively by the changes in weather and inconsistency in terms of labor availability (Stanczak, Wiczanowski, &Boche, 2016). Also, all modules being constructed using the off-site technique ensures that they arrive with a 95% completion rate as opposed to the traditional technique whereby completion of the project is dependent on weather conditions as a result of the construction processes taking place on the site. Contractors and manufacturers using the off-site technique must comply with different transportation regulations which vary from one state to another (Stanczak, Wiczanowski, Boche, &Stanczak, 2009).
According to Reveliotis (2005), the process of shipping assembled elements of a building from one site to another will need differing codes, permission, lead cars, and different associated costs. Contractors using the traditional on-site technique are often exempted from this challenge since most of the building processes occur at the site. Offsite construction may also require the deployment of special engineers to take care of the materials being shipped as opposed to a traditional technique where no material is usually transported from the primary construction site (Daniels, 2016).
Lastly, the traditional construction uses Critical Path Method (CPM) is the most common construction scheduling technique as opposed to the modern offsite construction which utilizes concurrent scheduling approach that overrides CPM. The CPM entails on-site sequential stacking of traders while concurrent scheduling requires a professional engineer to assess the entire process and determine its cost, the labor force to be acquired, and the supply chain to be used in management (Spooner & Smith, 2011).
Similarities
The main similarity that exists between traditional on-site and the current off-site construction industry is that construction processes usually begin at the same time in each concept. Secondly, these construction ideas occur all over the world despite some striking differences in popularity. The off-site construction industry has gained more popularity all over the world as compared to the traditional one which is gradually picking up due to some associated improvements. However, both manufacturers and contractors using an either technique must comply with rules, laws, and regulations governing the building and construction industry (Spooner& Smith, 2011).For instance, many states often require a third party agency or have a program responsible for the regulation of the building design as well as approval and inspection of the entire project until its completion period. The impact of these regulations, however, varies from one state to another.
Resource Allocation and Sequencing
According to Goodier and Gibb (2007), efficient allocation of resources is an essential step towards ensuring that the construction project achieves its objectives within the desired schedule. This concept helps in ensuring that resources available for the project are assigned appropriately with respect to the plan provided before the initiation of the entire exercise (Goodier& Pan, 2010). On the other hand, sequencing helps in ensuring that every resource is made available at...
Request Removal
If you are the original author of this essay and no longer wish to have it published on the customtermpaperwriting.org website, please click below to request its removal: