
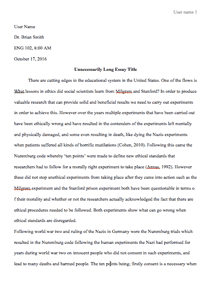
Leyland Trucks, a large manufacturing company situated in the town of Leyland, is considered one of the foremost manufacturing companies in the world. The company designs develop and manufacture light and heavy-duty trucks. To ensure efficiency in the production and customer service processes, the company has incorporated some values. These include teamwork, innovation, customer focus, empowerment, personal responsibility and personal development. To improve their production processes, the company has also applied various principles in their day to day activities. These are the principles of lean manufacturing and the Six Sigma program.
The Principle of Lean Manufacturing
The lean principle is a process incorporated by companies to reduce inefficiency and wastage of resources in the designing, development and manufacturing operations. The policy has been widely utilized in producing firms around the world. This is because the Lean principle uses improvement methods to eliminate waste and solving problems. Additionally, it streamlines processes to increase revenues. According to Bhattacharya et al., the policy makes it easy to expand efficiency within the organization through minimizing cots, maximizing profits, and improving overall efficiency (49). It streamlines processing and service processes to ensure quality delivery to customers. The goal of the lean principle is to eliminate components that do not add value to the manufacturing process. This is why the policy is widely used in countries where the production process is usually costly. Adopting this process enables companies in such countries to compete internationally with companies in countries where the production process is less costly. According to Kumar, the lean process incorporates five basic principles (155).
Perfection
A lean producer sets his/her objectives for perfection. The total quality administration is to efficiently and persistently evacuate the underlying drivers of low quality from the manufacturing operations with the goal that the plant and its products are moving towards perfection.
Flow
One exceptionally unique key to eliminate waste is flow. If the value chain quits pushing ahead for any reason, at that point, there will be a waste. The solution is to make a value stream where the product never stops in the process of production. Where every part of development and manufacturing is wholly synchronized with alternate components. Flow in the whole production process will tend to limit waste and increase the incentive to the client.
Value
Each organization needs to comprehend what value the client places on their services and products (Saleeshya et al. 544). The amount the customer wants to pay for the company's product depends on this value. This prompts a top-down target costing approach that has been utilized by manufacturing firms. Target costing centers around what the client will pay for specific services and products. From this, the necessary cost of these items and services can be resolved. It is the organization's business to reduce waste and cost from the production process with the goal that the client's price can be accomplished at an excellent benefit to the organization.
The Value Stream
The value stream is the whole flow of an item's life-cycle from the inception of raw materials used to make the item through to the client's cost of utilizing and at last discarding the item. Only by an examination and clear comprehension of the value stream and its value-add and waste can an organization genuinely comprehend the debris related to the designing, production, and delivery of an item. The lean principle advocates for manufacturer and client partnership and radical production network administration to eliminate waste from the whole value stream.
Pull
The best approach to guarantee that nothing is manufactured ahead of time is the pull approach (Sarwade 137). A pulled approach expresses that a company does not make anything until the point when the client orders it. To accomplish this requires incredible adaptability and short process durations of designing, developing and manufacturing of products. It likewise requires a system for informing each progression in the value chain what is expected of them then, in light of addressing the client's needs.
The Leyland Trucks company has improved the processes of manufacturing and assembly by incorporating the principle of lean. Lean procedures have led to improvement in the quality of products, an over twenty percent reduction defects in the production process, reduction in the waste of resources and faster manufacturing and assembling of products. Leyland has a high-level production process that helps it maintain the highest standards of production through a streamlined process.
Leyland uses the Paccar Production System whose core focus is developing people to ensure efficient and profitable business. The team bound method of lean manufacturing that provides total teamwork and production of market-driven products and services. It is driven by foundations such as empowerment, leadership, the organization vision, and encouragement. Leyland trucks utilize the lean manufacturing principle of pull approach by building to order.' This means that every day new orders are accepted, and the procedure is initiated that starts from the customer ordering a truck to create a bill of materials to the truck being built. The customer orders the truck, a bill of materials is created, a production slot allocated, communication made to the supplier and inbound flow and business communications made. The parts are then delivered, and the truck is assembled. The company also uses the Master Production Schedule (MPS) to make sure that all the suppliers supply on time and that the production teams are well organized and prepared regarding time, and workload cycles ensure that products ordered by clients are delivered on time. Markedly, the company provides that items to be delivered are communicated to the supplier six days before the delivery date. This saves time and ensures efficiency in the production process.
The Six Sigma Program
Additionally, Leyland Trucks has incorporated the Six Sigma program in an attempt to improve its manufacturing operations. The Six Sigma program combines some elements that bring about efficiency in a company's production process (Ray and Miglani 37). These include total customer satisfaction, quality in the operations of designing, development and manufacturing, process design, capability and control, evidence to eradicate defects, the DMAIC cycle and structured training, organization, and improvement process.
The benefits of the program rely on its information-driven approach and its emphasis on utilizing quantitative measures of how the framework is performing to accomplish the objective of process change and variation lessening (Pyzdek and Paul 233). That is done through the application of the Six Sigma improvement projects, which like this take the Six Sigma DMAIC arrangement of steps.
The DMAIC cycle is a disciplined methodology that includes Defining the problem, Measuring inputs and outputs, Analyzing by developing hypotheses to identify the causes and thus validate the assumptions, Improve production processes by coming up with improvement ideas and lastly Control that seeks to establish performance standards and dealing with any problems.
To incorporate the Six Sigma program a company has to train its employees to assume various roles of the Six Sigma as Leyland has done. According to Gandhi, there has to be the role of a Champion' which is taken up by the top management, the Master Black Belt,' the Black Belt' and the Green Belt' (11). The Champion manages the rest of the individuals in the other roles while the Master Black Belt assists those in the Black Belt to execute their functions correctly. Those taking up Black Belt roles should involve themselves in developmental changes in the organization while those in the Green Belt are tasked with managing Six Sigma projects.
Benefits of the Lean and Six Sigma Principles
The increase in profits through streamlined processes brings about efficiency. These principles ensure a company can produce more with fewer resources.
The decrease in costs through the reduction of wastes. Waste, in this case, refers to activities that are not required during manufacturing that comes at a price. Application of these principles also reduces costs through solving problems in different processes that cost an organization money.
Improve efficiency and effectiveness through maximizing satisfaction and proper allocation of resources.
Developing employees and people through the crucial involvement of employees in the organization's improvement process and building trust.
Section 2 Evaluate how the use of the ERP system may have helped to improve the efficiency and effectiveness of the operation at Leyland by preventing, avoiding and reducing various supply and scheduling issues
Nowadays, companies have to incorporate emerging technologies such as ERP to remain relevant in the ever-changing global market (Nour and Samar 104). To cover newly placed orders efficiently and in time, companies have to make sure that information is well organized and is real time. ERP systems are adopted in an attempt to acquire operational details faster, integrate information from various departments and help in reducing the cost of manufacturing. Leyland has utilized an ERP system to improve efficiency and effectiveness in its operations. ERP is Enterprise Resource Planning and incorporates various activities into one system to synchronize processes and information in a company. These activities include customer relationship management, human resources, accounting and order management and inventory.
ERP programming additionally offers some level of synchronized reporting and computerization. Rather than constraining workers to keep up free databases and spreadsheets that must be physically converged to produce reports, some ERP arrangements enable staff to pull reports from one framework (Bhoon 101).
Leyland Trucks has incorporated the ERP system majorly into their operations. Having developed different software for various transactions such as customer relationship management systems and e-commerce with suppliers. This system integrates all the manufacturing units, providing a complete view of the entire organization. Using a three-tier architecture, the system is flexible and scalable, giving the company lower inventory levels, real-time access to information, cost control through strategic sourcing and the optimized process runs. The project also involves a supply chain management system connecting around 1,000 suppliers of Leyland trucks through the web.
The ERP system has over time enabled the Leyland Company to become better organized to cover orders on occasion and efficiently. Incorporating the system has also allowed the company to attend to clients' issues and needs faster thus proving efficient. This has helped improve the company's public image as well as the relationship. Faster delivery of ordered products which is also as a result of adopting the ERP system has brought about better customer satisfaction. The accuracy of the information from the ERP system has enabled the company to become more flexible and to utilize resources efficiently. Knowing what particular requirements a client wants has helped the company to get deliveries from suppliers faster and hence reduce the period taken between when the client orders a product and when they receive it. The scheduling issues that were previously being witnessed due to lack of a particular item during the manufacturing or assembling process are no...
Request Removal
If you are the original author of this essay and no longer wish to have it published on the customtermpaperwriting.org website, please click below to request its removal: