
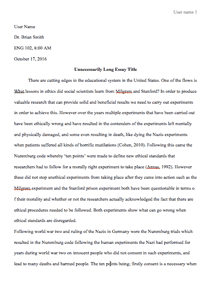
The progress in the global market is increasingly pressuring companies to boost the efficiency of their processes. Notably, warehouse management is no exception. Therefore, many businesses are embracing lean principles that will upgrade warehousing and improve organization and product flow and their ability to satisfy the demands of consumers. However, it is essential to understand the meaning of warehouse management and the significance of lean principles in warehouse management. Therefore, this paper seeks to enlighten on the aspects of lean warehouse management and why businesses to adopt it.
Warehouse Management
According to Bradbury (np), warehouse management is a structure that sustains the daily operations of a store. Today, stores perform two major operations, namely, managing the movement of materials within the facility and controlling the flow of data across the supply chain. In particular, an efficient warehouse management structure aids businesses by supporting the need for custom orders and tracking stock from arrival time at the store until it reaches its final destination. Similarly, it enables companies to resupply inventory based on client demand and maintaining the warehouse to protect commodities. Nevertheless, a growing inclination for pick-and-choose orders and a shifting market have resulted in new challenges for warehouse management. Consequently, stores cannot stockpile goods while waiting for consumers to buy from their predetermined supply. Instead, warehouses must consistently move new products to meet the ever-changing demand.
The main challenges that warehouse management encounters include poor layouts, inefficient storage, and movement of supplies, inefficient systems, and reoccurring slow phases in the supply chain. First, poor design refers to the organization of the warehouse. For instance, some storage spaces may be overfilled or others underused, which makes it cumbersome to locate supplies (de Visser, 4). Similarly, if there is too much space between workstations, the time taken to move orders between stations increases. Additionally, a poor layout may force workers to reach, bend, or stretch excessively to finish their tasks. Second, regarding inefficient storage and movement of supplies, fast-moving goods might be stored in a difficult-to-reach space, which increases the time and labor needed to resupply picking lanes. Third, the inefficient process may lead to poor stock managements, damaged or lost items, and mislabeled goods (Bradbury, np). Finally, concerning slow durations in the supply chain, workers often have to wait for resupply of materials before the processing of shipments. Similarly, approvals for purchases or new materials can take too long to process and backup of orders. Consequently, implementing lean warehouse management can benefit businesses extensively in eliminating these challenges.
Lean Warehouse Management
Lean warehousing applies various lean manufacturing techniques to overcome challenges facing storage management. In particular, it is the way of the future that implements the Value Stream Mapping, Kanban, and the 5S strategy that aid in accomplishing a primary objective, namely, making problems visible (Mustafa, 3).
Value Stream Mapping (VSM)
VSM is a process that empowers warehouse managers to understand the current processes of the warehouse. Notably, it maps out visually the workflow and identifies clearly the relationships among operations, which enables store managers to comprehend how different processes interact, to see the effect of scheduling and departmental workflow on processes, and to identify possible gaps in their systems (Bradbury, np). Consequently, the managers can recognize materials that are stored ineffectively or handled more often. Similarly, they can enhance the warehouse layout and storage structure to minimize material handling and improve storage.
5S
Notably, having a clean and organized store is all about having efficient warehousing operations, proper communication, and excellence in training. A warehouse should identify problems quickly, tackle their root causes timely, and curb recurrence. The 5S strategy plays a significant role in improving efficiency in a warehouse through the identification of such issues and bringing them to the surface for timely resolution. The 5S Lean strategy applies the sort, set in order, shine, standardize, and sustain approaches (Muraira et al., 5). First, sorting includes removing unnecessary items from the workstation. Notably, warehouses can maximize space by discarding unneeded tools, equipment, and supplies, which increases the available storage space and work area.
The second S refers to setting in order what remains after discarding the unnecessary items, which entails arranging each unique work area for convenience and efficiency. In particular, it is essential to organize workstations, supplies, and equipment in a manner that will enhance worker productivity, mainly, the movement from one area to the next and minimize tiring movements such as reaching, stretching, and bending (Mustafa, 7). In this step, lean warehouse management employs ergonomic strategies such as semi-circle ranges to facilitate lefty-righty switches. The third phase involves employees cleaning their work area after every shift. Mainly, this approach is designed to aid staff to identify potential problems by removing clutter and debris that make spotting problems difficult. Additionally, cleanliness contributes to a standard of behavior and signals order as a presumption of the warehouse. Therefore, daily sweeps as part of the lean warehouse management can comprise safety inspections that lower liability and equipment maintenance checks, which raise equipment longevity.
On the other hand, standardization includes documentation of successful improvements, which enables easy application in other workstations. An excellent example standardization is the use of standardized labels in the lean warehouse. Labels with all the relevant information for any products in the store will increase efficiency significantly. Additionally, eliminating waste is a critical aspect of lean warehousing. Therefore, standard labels should discard unnecessary information or debris (de Visser, 10). Similarly, standardization also pertains to a value-driven culture in which core values consistently drive the behavior of staff. The final step for successful lean warehouse management is the sustaining phase. The step requires that each step in the 5S be repeated daily, which ensures that the management systems improve work practices on a regular basis.
KanbanThis pull system pulls supplies to the warehouse floor depending on what clients have ordered and the work that has been finished. It uses visual cards to control the workflow within the supply chain. Consequently, it improves processing duration by developing an orderly and continuous flow of materials from picking, packing, and shipping (Bradbury, np). Additionally, it aids in minimizing errors in processing since it restricts work-in-progress. For example, new work cannot commence until the current job is finished and moved to the next work area. Consequently, workers can identify problems and prevent errors from recurrence.
Benefits of Lean Warehouse Management
According to Puto et al. (3), there are various reasons why lean management is essential for any warehouse. First, the repository manages to meet the varying needs of their clients by improving their efficiency. Second, lean warehouse management enables stores to pull supplies based customer demand. Third, through sorting, warehouses maximize the space available for supplies. Fourth, when a warehouse implements the Kanban strategy, it reduces errors in processing because the approach controls work-in-progress. Additionally, lean management minimizes labor costs linked to rework and inefficient handling of items, reduces order processing time through the standardization of workflow and limited work-in-progress (Puto et al., 5). Finally, lean management minimizes unnecessary transportation of supplies by storing items based on their move.
Conclusion
To conclude, the global market is growing rapidly, and businesses need to keep up with the growth if they intend to remain in operation. Therefore, the companies need to improve efficiency in their operation. Lean warehouse management through its lean principles helps to upgrade warehousing and improve organization and product flow and the businesses ability to satisfy the demands of consumers. The importance of lean warehouse management arises from the benefits it accords firms that implement it.
Work Cited
Bradbury, Joel. What to Know About Lean Warehouse Management. Industrial Distribution. N.p., 2017. Web. 8 May 2017
de Visser, J. Jeffrey. "Lean in the warehouse." (2014).
Muraira, Etna, Lorena Garzafox, and Bernardo Villarreal. "Increasing Customer Satisfaction Through Lean Distribution." Proceedings of the 2014 International Conference on Industrial Engineering and Operations Management. 2014.
Mustafa, Muhammad Salman. A Theoretical Model of Lean warehousing. Diss. Politecnico di Torino, 2015.
Puto, Agnieszka, Katarzyna Brendzel-Skowera, and Helena KoA. "The Significance of Lean Culture in Warehouse Management." Proceedings of International Academic Conferences. No. 1003976. International Institute of Social and Economic Sciences, 2015.
Request Removal
If you are the original author of this essay and no longer wish to have it published on the customtermpaperwriting.org website, please click below to request its removal: