
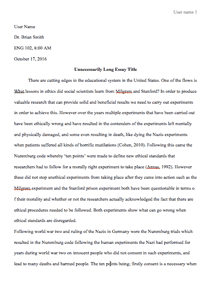
Evaluation of the implications related to the management of operations within an organization that carries out its activities internally necessitates consideration of factors such as the products and services demanded by customers, the environment, as well as cultures and resources (Hanim et al. 2012). These may be followed closely by determination of the strengths and weaknesses of the organizations which are necessary for the formulation of the vision articulated through the mission statement. Most importantly, the organizations mission statement focuses on expressing the aspirations and values as well as the purpose and reasons as to why it exists. Nonetheless, the basis for the existence of this organization entails the development and formulation of the organizations business strategy (Jones & Robinson. 2012). However, the business strategy employed entails a long-term plan that aims at accomplishing the mission designed in the mission statement. Additionally, the functions of each activity carried within an organization facilitate in the derivation of the strategy in support of the business strategies that entail marketing, finance, operations, just to mention a few. Nonetheless, the organizations which carry out their operations internally face a variety of challenges in the management of their activities (Jones & Robinson. 2012). Therefore, the essence of the current paper entails determining the implications associated with operations management in organizations that carry out their internally. This will be followed closely by the selection and assessment of a similar type of product from two firms involved in internal operations and a description of the production processes, customer interaction and technologies employed. Moreover, the paper will focus on describing each of the organizations movement towards lean processes or six sigma and their impact on the culture, efficiency, and success of every firm.
Discussion
The past few years have been characterized by a surge in the activities related to the effects of operations management particularly in service-oriented organizations. The emphasis on these activities has brought about the evaluation of how and where management of operations has influenced the performance of service firms. Nonetheless, according to research, operations management describes the ways in which organizations employ different strategies in the production of their goods and services (Stevenson, 2018). Similarly, research indicates that after the mass production paradigm, there has not been another other approach developed with the aim of operations management. Some of the popular approaches employed include flexible specialization, lean production, mass customization and agile manufacturing. In the flexible specialization, the organization focuses on separate parts of the value-adding process through collaboration within networks for the production of whole goods and services (Jones & Robinson, 2012). Nonetheless, the networks employed should be highly developed, utilize effective processes in the collaboration and development of long-term relationships between organizations.
Moreover, lean production emphasizes on the eradication of all forms of waste from a production system through driving inventory levels down and exposing inefficiencies, reducing costs and cutting lead times (Thomas et al. 2014). The other popular approach entails mass customization which aims at combining high volume or rather a mass production with adaptive gods and services to meet the requirements of individual customers (Elking et al. 2017). Lastly, agile manufacturing entails operations which focus on the need for an organization to have the ability of frequently switching from one market-driven objective to another.
Some of the implications obtained from the management of operations in organizations that operate internally include strategizing their activities towards the realization of the mission. This occurs in three different ways namely cost leadership, differentiation, and response. These tasks are turned into tasks that need to be completed with the aim of delivering goods and services that are better, cheaper and in a more responsive manner (Cherrafi et al. 2016). Cost leadership focuses on what the customers perceive to be the maximum value which occurs through driving down prices without necessarily lowering the quality of the products. This occurs through the allocation of resources, shifts, and routes as well as turnover times. These factors allow the customer to save some money without necessarily understanding why (Cherrafi et al. 2016). However, the reduction of cost leadership necessitates alignment with the strategies, mission, and goals of the organization.
Similarly, differentiation of the products within such organizations requires setting up the goods and services in a distinct manner from the competitors. The main aim of differentiating the products entails the identification of the elements that add value to the customer regarding quality, accessibility, or follow up on customer service as well as repair and maintenance (Albliwi et al. 2017). Furthermore, response entails a broader view that not only focuses on the delivery of goods and services to customers but the ability of the organization to adjust to other factors or changes in the marketplace on time. It also refers to the set of values associated with flexible, rapid and reliable performance (Chakraborty & Kay Chuan, 2013). For instance, one organization that employs these factors entails IKEA, the leading retailer of furniture across the world. The management of operations at IKEA occurs through understanding the market as well as its customers through the design, production, and delivery of products and services in the right manner. The survival and success of IKEA in the market in the long-term necessitates supply of products and services effectively. Most importantly, some of the activities that guarantee the company's success and are related to operations management include the arrangement of their store's layout in a way that gives a smooth and effective flow of customers, also referred to as process design (Garate, 2013). These are followed closely by product design which requires developing stylish goods that can be flat-packed in an efficient manner. Additionally, IKEA employs services such as coping with fluctuations in demand through capacity management, maintenance of safety and cleanliness with the aim of preventing failure and the management of inventory through avoidance of running out of products for sale (Hanim et al. 2012). These are coupled with the enhancement and monitoring of quality of services to customers and continued examination and improvement of their operations.
Selection and Assessment of a Similar Product from Two Different Firms
According to research, operations management entails the use of resources in an appropriate manner that facilitates the creation of outputs that fulfill the defined requirements of customers and the market. For instance, the production of goods such as smart phones between the Apple Company and the Samsung organization necessitates the delivery in an efficient and effective manner (Hanim et al. 2012). On the one hand, the production process employed in both organizations entail an input-transformation-output procedure. This process focuses on taking in a set of input resources which are essential for transforming something into outputs of products and services. However, despite the fact that the operations carried out in these organizations conform to this general process, there exist differences in the nature of their specific inputs and outputs (Haddad et al. 2016). On the one hand, the production process employed by Samsung entails outsourcing some their operations from manufacturing firms located in other states. The various inputs used in the production of a Samsung phone are manufactured in states such as Korea where the costs are relatively cheaper as compared to the host country. Similarly, Apple employs a similar strategy in the production of their goods (FastCap, 2014). However, the difference in the production processes employed in both countries entails specification of the market, product design, and customer interaction.
According to research, the production of smart phones particularly in the 21st century entails a competitive endeavor that requires organizations to strive towards meeting the requirements of their customers (Elking et al. 2017). The achievement of such objectives occurs through interaction with the customers to better understand their requirements, and the products they wish to get from the company. Nonetheless, the Apple and Samsung companies employ similar strategies in reaching out to their customers and implementing their insights in the production of desired goods. However, according to research, Samsung has recently received a drawback after one of its products was recalled for repair and maintenance after bringing about severe effects to the customers (Deshmukh & Chavan, 2012). Since then, Samsung has focused on the production of quality goods to remain relevant and competitive in the industry. Moreover, the other difference between the production process and customer interaction techniques employed within these two companies entails the measurement of quality. The Apple Company measures the quality of their products through the integration of hardware software and services (Chakraborty & Kay Chuan, 2013). Contrastingly, the Samsung Company focuses on quality through the employment of the six sigma strategy that emphasizes the experiences of their customers and reduction of costs.
Besides, the movement of Apple and Samsung towards lean processes and the six sigma program entails application of similar goals such as the elimination of waste and the creation of the most efficient systems and products. However, the difference in the approaches used entails the distinct identification of the cause of waste (Cherrafi et al. 2016). On the one hand, the Apple Company employs the lean manufacturing process that ensures that the production processes are relatively high in a way that each step naturally follows the next thereby resulting in minimal waste. This process allows the company to eliminate waste that may occur through waiting, overproduction, transportation, over-processing, high levels of inventory and the identification and fixing of defects. The application of this process boosts the culture, efficiency, and success of the organization through the development of products that focus on meeting the needs of the future (Haddad et al. 2016). For instance, the Apple Company has streamlined their production processes as well as their goods and services in a way that eradicates the technologies that do not add value. It has also allowed the company to create products which are simple, user-friendly, innovative, sophisticated but efficient.
Additionally, the application of the six sigma strategy at Samsung has facilitated the culture, efficiency, and success of the company through allowing the employees to move materials less frequently thereby improving the quality and ensuring minimal inventory (Haddad et al. 2016). These may be followed closely by the facilitation of dealing with quality issues during the manufacturing process thereby saving the organization time and resources because employees are not struggling to fix the defects at a later stage (Elking et al. 2017). Most importantly, the application of the six sigma manufacturing process brings about success to the company due to factors such as timely production and delivery, satisfying experiences from the customers and development of goods at a higher standard of quality....
Request Removal
If you are the original author of this essay and no longer wish to have it published on the customtermpaperwriting.org website, please click below to request its removal: