
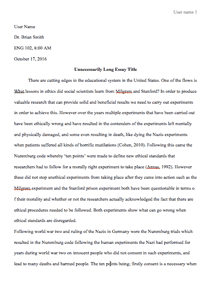
Physical agents refer to energy fonts that are recognized to cause distress to people by either can leading to illness or hurt their human body. The examples of physical agents include; Noise, Vibrations, electromagnetic fields and extreme of temperatures. The effects of this physical agents, exposing one to the extreme sound for an extended period, this could cause a partial or p permanently or deaf. Noise sounds are unwanted sounds comes from machines that cause the steady loss of hearing to human ears in the long run. This damages their ear drum thus if it's not taken good care in the hospital it causes partial deaf. Vibrations refer to continuous movement or shaking back and forth of the body a worker at a factory. Many organizations use both light and heavy machinery that during the processing process the machine vibration can cause lower back pains to human resource. A mechanical vibration affects the hand-arm when a hand touches the device while the whole body vibration is generated when vibration is transmitted through seats and feet at the work station. Electromagnetic fields refer to particles, x-rays, and atoms emitted from the factory which can have long term effect for poorly dressed company employees. Extreme of temperatures refer to cold and warm temperatures in various sections in the factory. Extreme Heat temperatures in plant sometimes can be deadly to workers. This paper aims to explore the administrative and legislative control of physical agents within their particular state.
Keywords: Noise, vibrations, Electromagnetic Field and Extreme of temperatures
This paper explores the administrative and regulations control of physical agents within your country. It further focuses the enacted laws of employee safety from Trinidad and Tobago and compared these laws with to laws from England and those from the EU in general on health and safety at work. Further, formalize with the current laws enforced in my country in dealing with the physical agent. Explore the enactment provisions legislated in my homeland and if they are complied with in working stations. Do an evaluation of legislation or enacted provisions for control of physical agents in the place of work.
Trinidad and Tobago law Vs. England and EU, health and safety provisions
In Trinidad and Tobago legislation on the employee, protection is stipulated in the country's constitution. The employer is responsible for the safety against Noise, vibrations and extreme of temperature while an employee at the factory. The management is required by law to provide safety signs o and risks while at the plant. It's responsibility for the company to protect workers against noise through giving them helmets and hearing protectors to protect employees against objects and noise in the factory (Daniel & Elvis, 2003). It further suggests that organization should ensure that these employees are trained and equipped with the necessary skills on machine handling and inducted on general safety requirement while at the factory. Visitors to the manufacturing site for purposes of a study should first be inducted on safety measures and be recommended suitable protection and clothing. The protective garment serves the purpose of ensuring that all employees are safe from any injury or danger. The supervisors should certify and provide an update to management on safety standards records on cases at the factory (Daniel & Elvis, 2003). Transmission machines should be fenced to reduce hazards. Prime movers, some parts of communication machines and running belts and wheels of the machines should be enclosed.
The legislations in England, on the other hand, adopted on 25 June 2002 Directive 2002/44/EC on the least health and safety necessities regarding the exposure of workers to the risks arising from physical agents (vibration, noise and extreme of temperatures). The report introduced protective measures of human resource from the risks which result from noise owing to its effects on the health and well-being of employees, mainly hearing damages. These rules were intended to ensure the health and warfare of every employee on an individual basis, but also to create safety for all Public personnel to avoid possible falsifications of competition. The employer should assess and measure the levels of exposure to noise to which employees are exposed. This is strict to be done in adhering to the Framework Directive 89/EEC. The results of the risk assessment are recorded on a regular basis and kept up to date. During the risk assessment, the employer is required by law to give attention to type or level, and length of acquaintance, exposure limit / exploit standards, unusual health effects. Spreading from a particular sensitivity of the employees, interfaces with other risks (none/toxic constituents, vibrations), the exposure to sounds past usual working 8 hours under factory responsibilities, and noise caused by warning signals at work stations.
The employer is obligated to eliminate hazards arising from exposure to noise or reduced it to a minimum. The reduction of threats resulting from exposure to noise shall be based on the overall principles of hindrance set out in Directive 89/656/EEC. Example the effective approaches or use of gear that involve less disclosure to noise, proper use of instructions on the accurate use of apparatus, procedural measures (shield, sound enthralling coverings) or organizational action to reduce duration and intensity of exposure the noise. In case this risk cannot be put into control then the employer should provide personal protective clothing and equipment to ensure health and safety of workers from physical agents. Exposure limits should always be monitored so as do not exceed set limits if the exceed its employer responsibility to put adequate measures to reduce the exposures.
Safety and health on manual handling
Manual handling is the process which involves human body parts in lifting loads at the factory. According to health and safety standards has stipulated weight limits for both men and women can raise in a work place. Referring to this legislation people weigh limit is set at 50kgs which is considered safe for any regular spinal cord can carry comfortably. Women on another hand the weight limit one can carry comfortably is 30kgs for regular spinal cords women works. It upon the employer to keep routine medical checkup on employees to ensure only those fit are only at work station. Weights above 30kgs and 50kgs it's the responsibilities of the employer to provide forklifts, sack trucks, trolleys and conveyors to the natural, safe handling of loads beyond 30kgs and 50kgs respectively.
Safety needs for employees working with the physical agents
According to 89/656/EEC, all Employee European countries should also undergo adequate training and induction on machine operation and the equipment handling. The organization should also ensure that these employees attain the age of 16 years or above and have adequate knowledge and skills on industrial operation and safety. The industrials standard working hours is 8.During this time the employer should give protective equipment's like protective hearing to protect employees from excessive noise, give protective clothing to guard workers against radiation and extreme cold from freezers. All responsibility for the safety of all employees is solely on the employer to ensure proper working conditions of employees at the work place.
The health hazards as per occupational hygiene
Occupational hygiene refers to the discipline of forestalling, identifying, gauging and controlling health hazards in the operational setting with the impartial of defending employee health and well-being and safeguarding the society as a whole. Health hazards: chemical agents include vapors, fibers, gases, dust, mists, and fumes. Physical agents include: vibration, noise, heats lighting and cold. Biological agents are bacteria and fungi.Ergonomic factors are stretching and lifting. Psychosocial factors, work load and stress. It's advisable for the organization to anticipate health hazard in place of work before it occurs. Recognition of health hazard chemical, physical agents, biological agents or adverse ergonomic situation that may pose health.Evaluation is necessary to certain the extent of exposure to the chemical hazards, natural or biological agents in place of work. This often encompasses measurement of the individual exposure of a worker to the risk/agent in the workplace. Control by procedural and engineering other means where the evaluation meditates. World health organization estimate that nearly 2 million work related deaths per year. While 386,000 deaths are as a result of exposure to airborne particulates and 152,000 deaths results from carcinogens in the place of work. Further, it indicates 37% of lower back pain is attributed to work.
Administrative preventions controls Measure
Risks should be eliminated and (if not possible) reduced by taking precautions, in order of priority. The basic BS OHSAS 18001 management system.The five steps are: elimination, substitution, engineering control and administrative control.If the risk is removed, all the other management controls, such as workplace monitoring and surveillance, training, safety auditing, and record keeping will no longer be required.
Â
Â
Bibliography
Authority, Health, and Safety. Physical Agents. http://www.hsa.ie/eng/Topics/Physical_agents/.
Bohne, Barbara A, and Harding, Gary W. Noise-induced hearing loss. http://www.oto2.wustl.edu/bbears/noise.htm.
Daniel, Alvin C. 2003. Control of Noise in the music industry in Trinidad and Tobago. December 2003. 2005. Elimination or control of exposure to vibration at the workplace. legislation.gov.uk. 2005. http://www.legislation.gov.uk/uksi/2005/1093/regulation/6/made.
IOM. OCCUPATIONAL HYGIENE. http://www.iom-world.org/services/occupational-hygiene/.
Labour, United States department of. Recommended Practices for Safety and Health Programs. http://www.osha.gov/shpguidelines/hazard-prevention.html.
2015. Laws of Trinidad and Tobago. Occupational Safety and Health Act. December 31, 2015. http://www.legal affairs.gov.tt.
Malchaire, Professor J. SOUND MEASURING INSTRUMENTS. [Online] www.who.int/occupational_health/publications/noise6.pdf.
2013. Manual Handling. Healthy working lives. [Online] April 18, 2013. http://www.healthyworkinglives.com/advice/work-equipment/manual-handling#legal.
nibusinessinfo.co.uk. Health and Safety Law in Europe. [Online] http://www.nibusinessinfo.co.uk/content/health-and-safety-law-europe.
Noise Induced Hearing Loss. HEW. http://www.agius.com/hew/resource/nihl.html.
2015. Occupational Safety and Health. [book auth.] LAWS OF TRINIDAD AND TOBAGO. 2015, pp. 55-57.
Presbycusis. Hearnet. http://www.hearnet.org.au/hearing-problems/presbycusis.
Sound Theory. http://acoustics.no/sound_measurement/sound_theory/.
Tekele Tadesse, B.Sc. Mengesha Ademassu, M.D. Kebede Faris M.Sc. Occupational Health, Safety, and Hygiene. [Online]
Triaxial -Human Vibration Meter. http://www.MMF.de.
TUC. EU Membership and Health and Safety Benefits. [Online]
Vibration Control. ACE. http://www.acecontrols.com/us/products/vibration-control.html.
Â
Â
Request Removal
If you are the original author of this essay and no longer wish to have it published on the customtermpaperwriting.org website, please click below to request its removal: