
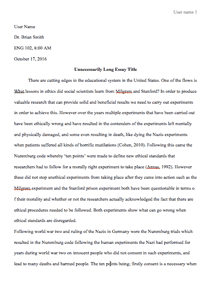
Natural Rubber (NR) is a renewable resource composed of the polymers from the isoprene organic compound, alongside other minor organic compounds impurities and water. The process of modifying the NR is meant to change the properties of NR in order for it to become applicable in the standard areas. The NR modification process through epoxidation of natural rubber produces an epoxidized natural rubber (ENR) which has an enhanced characteristic which varies in terms of the degree of epoxidation. Basically, epoxidation is the change of the normal unsaturated compound to an epoxide. Epoxidation of the NR leads to an increase in the polarity of ENR. While the polar epoxide groups found in the ENR leads to the compatibility of the rubber with silica, which is a highly polar filter.
Figure. Chemical form of epoxidised natural rubber
Â
Materials
Epoxidized natural rubber (Ekoprena-25), with 25% epoxidation
Neo cis BR40 Neo cis BR40
Highly dispersible silica, Zeosil 1165MP with CTAB surface area of 164 m2 /g,
4% of Silane coupling agent, bis(triethoxysilylpropyl) tetrasulfide (dry blend in ratio 1:1 with carbon black)
Methods
The compound used in this process was truck tire tread based, and the expression of its formulation was according to the parts s per hundred of rubber (phr) as illustrated in the table bellow
Table 1
Ingredients NR/BR-CB ENR-silica ENR-silica-CB
NR 70 - -
BR 30 - -
ENR (Ekoprena 25) - 100 100
Silica - 55 50
TESPT (X505) - 4.4 4.0
Carbon black, N234 53 5 10
*Mixes also contain the ingredients ZnO 3, stearic acid 3, calcium stearate 2, 6PPD 1, TMQ 1, TDAE oil 8, wax 1, sulphur 0.7, TBBS 1.5 and TBzTD 0.25
Internal mixer GK70 with the capacity of 50 liters was used for mixing, the table below illustrates how the fill factor of the mixer was filled at 0.7.
Table 2. Mixing procedure
Time (min) Ingredients
0 Rubber
1 filler, silane**
2 filler, silane**, oil
3 sweep
4 powder
5 dump
**Only for silica compound
After the batches were dumped, they were sheeted out in form of a two-roll mill. Due to the high Mooney viscosity, the process was followed by the re-milling stage of mixing, which was performed on a silica master batches inside GK70. At the controlled batch temperature of below 1100C, mixing of curative was done in the final stage of mixing GK70.
Testing
The measuring of cure characteristic was done over 30 min at a temperature of 1500C and at an arc of 0.50 using Alpha Technologies MDR2000. While at the temperature of 1200 and 1000 respectively, scorch and Mooney viscosity was tested, using the viscometer MV200 from Alpha Technologies.
The measurements for BRC, bound rubber content, were executed on an unsecured sample which involved the use of toluene in an extraction of the unbound rubber at the room temperature, at the period of seven days in both ammonia and normal environment. Additionally, the BRC ammonia treatment was completed to get the chemical bound rubber while there was cleaving of ammonia physical bonding between silica and rubber. The calculation for BRC (g/g filler) was as follows:
BRC(%)=Wdry-WinsolWoxWfiller.phr W total.phr X 100
W0= Samples initial weight
Wdry= extracted samples dry weight
Winsol= insolubles weight (mainly filters)
Wfiller,phr= aggregate filler weight in phr
Wtotal,phr= total compound weight in phr
The aggregate BRC is defined as BRC acquired from normal atmosphere whereas the chemically BRC is the data found from the measurement of the BRC ammonia treatment. The preparation of the Vulcanizates is done using the electric press at 100 bars, by curing of the compounds according to their t95 at 1500C. The ISO-37 principle was applied in the measuring of the vulcanizates' Tensile properties and DIN-53505 was used in determining the hardness of the cured samples. The law of ISO4649 together with s Akron abrasion test was used in conducting the abrasion resistance.
Dynamic properties of vulcanizates: Mettler Toledo Dynamic Mechanical Analyzer was used to measure Loss modulus, strong modulus together with glass transition temperature.
Â
Request Removal
If you are the original author of this essay and no longer wish to have it published on the customtermpaperwriting.org website, please click below to request its removal: